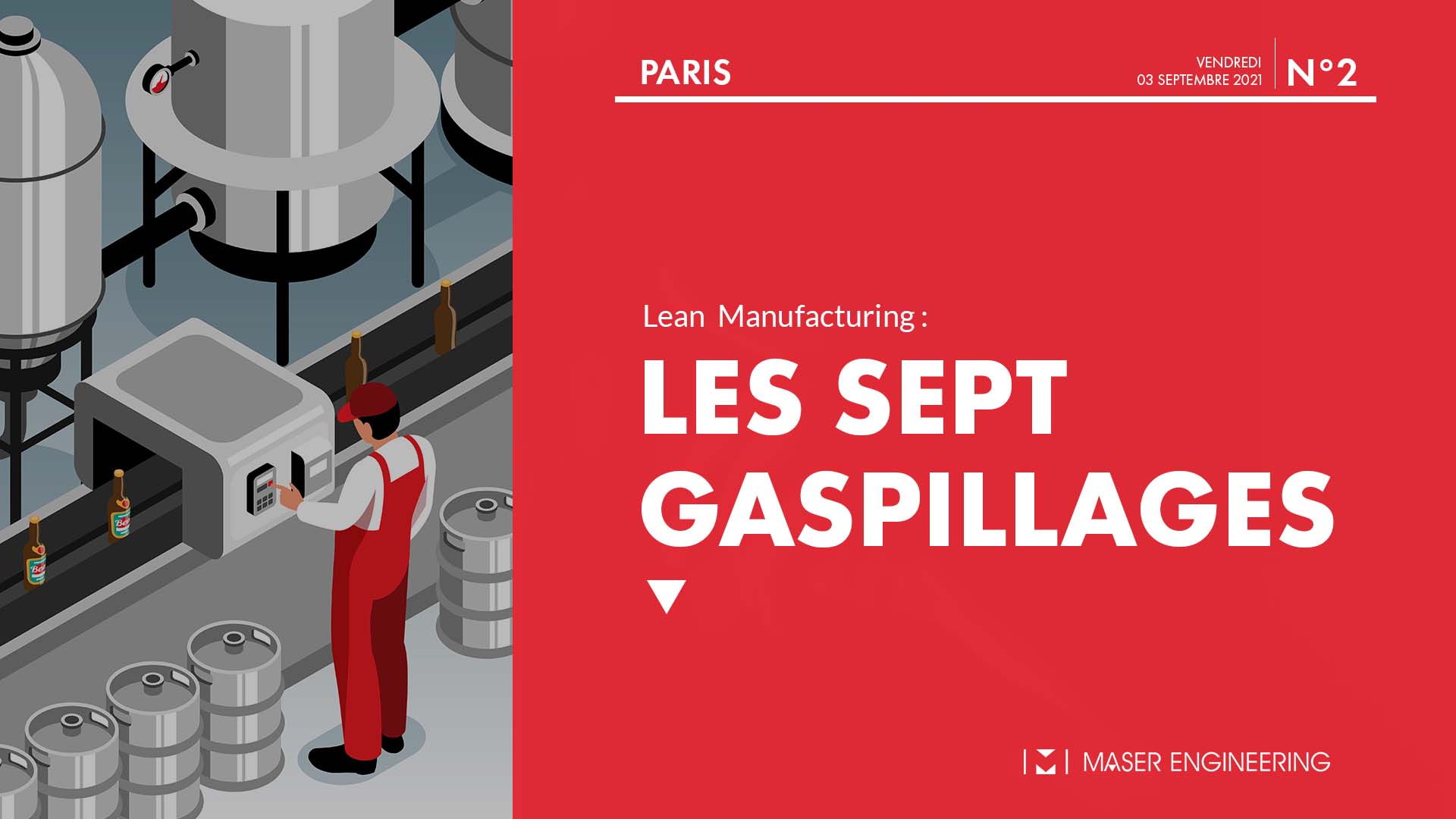
Dans un environnement particulièrement concurrentiel, les industriels se doivent aujourd’hui de produire de façon efficace en limitant les coûts. Dans le cadre d’un processus d’amélioration continue, il est d’important d’éliminer tous les types de gaspillages présents dans un processus de production. C’est là qu’intervient le Lean Manufacturing.
Qu’est-ce que le Lean Manufacturing ?
Le Lean Manufacturing est une méthode permettant l’élimination des gaspillages au sein des processus de production, dans le but d’éliminer successivement la non valeur ajoutée, pour obtenir une meilleure flexibilité de l’atelier de fabrication.
Le Lean regroupe les 7 principaux domaines dans lesquels se trouvent les activités « Muda* » plus communément connu sous « Les 7 gaspillages». L’élimination de ces gaspillages est primordial pour la réussite de l’entreprise. Ils peuvent réduire la rentabilité, diminuer la qualité, augmenter le coup de production, et parfois même, la satisfaction des employés. Pour ces raisons, il est important d’identifier les activités n’ajoutant aucune valeur, dans le but d’améliorer le processus dans lequel elles sont présentes, afin de les éliminer.
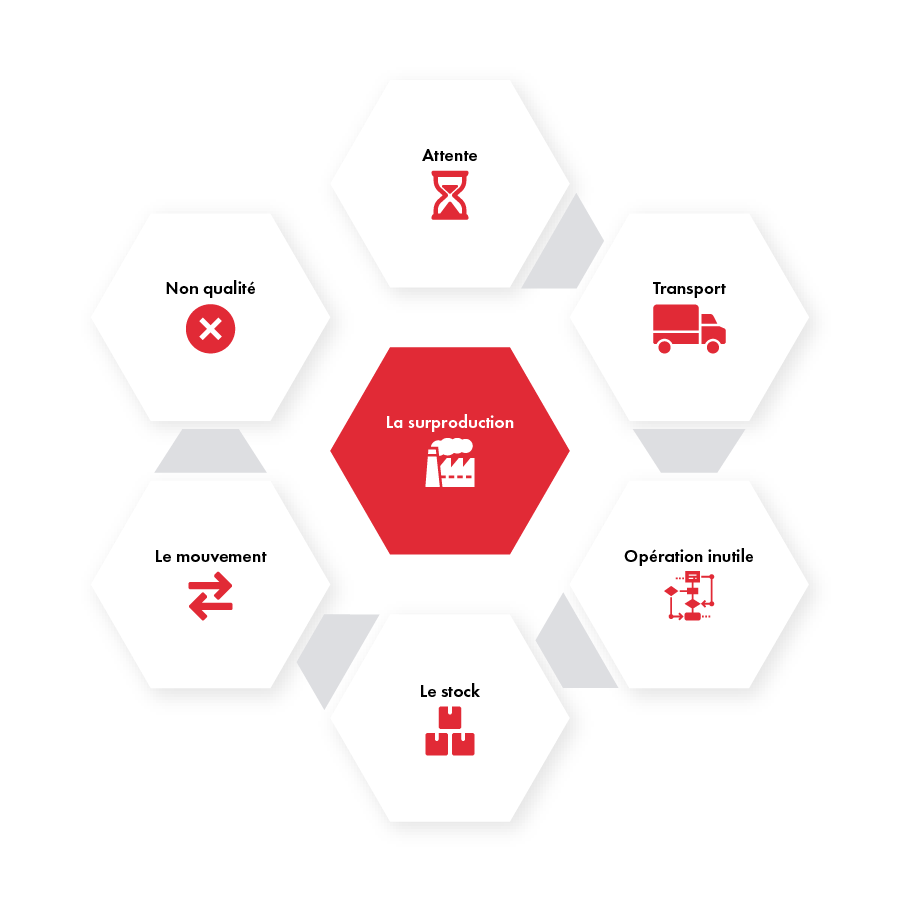
Voyons ici le descriptif général de ces 7 gaspillages :
1. Surproduction
Le gaspillage correspond ici au surplus que le client ne souhaite pas payer. Produire plus, signifie que vous excédez la demande du client, ce qui entraine des coûts supplémentaires. La surproduction d’une certaine façon, déclenche l’apparition des 6 autres gaspillages. Produire plus, nécessite davantage de déplacements supplémentaires, des temps d’attente plus long etc…
Exemples de surproduction :
- Taille de lots inadaptée.
- Produire un trop grand nombre de pièces
- Double saisie d’indicateur
2. Surstockage ou stock inutiles
Les stocks excessifs sont souvent dus aux sociétés gardant du surstock afin de répondre à une demande inattendue, se protégeant ainsi contre les retards de production ou les fabrications de mauvaises qualités. Ces stocks excessifs répondent cependant rarement aux besoins du client et n’ajoutent aucune valeur, augmentant simplement l’entreposage et les frais liés à l’amortissement.
Exemples de surstockages :
- Stock en surplus suite à de mauvaises prévisions de ventes.
- Produits détériorés ou périmés sur le lieu d’entreposage.
- Mauvaise estimation des besoins
3. Transports et déplacements inutiles
Ce sont tous les déplacements inutiles d’un point A à un point B de la matière ou des collaborateurs. Le déplacement constant des matériaux peut s’avérer coûteux pour votre entreprise et nuire à la qualité. Il est donc préférable de réorganiser son espace de travail pour réduire les déplacements inutiles.
Exemples de transports :
- Opérateur devant passer d’un poste à l’autre, ceux-ci étant trop éloignés
- Stockage intermédiaire qui nécessite 2 transports
- Formation éloignée du lieu des participants
4. Surprocessing ou traitements inutiles
Il s’agit des tâches supplémentaires que l’on réalise sur un poste ou sur l’ensemble du processus. Ces contrôles, en Lean, sont des tâches à non- valeur ajoutée. Le client n’est pas prêt à payer ces contrôles, voulant de la qualité dés le départ.
Exemples de surprocessing :
- Trop de contrôles dans le processus de fabrication
- Programme informatique compliqué à utiliser
- Tableaux de bord complexes avec trop d’indicateurs inutiles
5. Mouvements inutiles
Ces mouvements représentent tous les mouvements faits sur le poste de travail, dans la zone ergonomique du collaborateur. On fera souvent référence à des problèmes ergonomiques.
Exemples de mouvements inutiles :
- Caisse à outils incomplète, nécessitant plusieurs allers-retours du technicien de maintenance.
- Besoin de se déplacer pour collecter des informations.
- Les déplacements inutiles, tels qu’aller à un point A pour rien
6. Erreurs, défauts et rebuts
Ils peuvent apparaître à chaque étape de la vie d’un produit : du moment où l’on conçoit le produit jusqu’à celui où on l’envoie au client.
Exemples d’erreurs :
- Produit non-conforme aux exigences du client
- Bugs informatique
- Casses, accidents
7. Temps d’attente et délais
C’est le temps passé à attendre un collaborateur, avant de pouvoir effectuer une action sur son poste, ou qu’un produit attend sur une machine.
Exemples de temps d’attente:
- Opérateurs inactifs lors d’une panne machine par manque de formation ou d’instructions précises.
- Opérateur attendant qu’un autre collaborateur lui apporte ce dont il a besoin.
- Temps de traitement de calculs.
Garant de l’amélioration continue, MASER ENGINEERING accompagne ses clients dans leur démarche de Lean Manufacturing, en diminuant le gaspillage et les pertes de non-valeur ajoutée, garantissant ainsi à ses clients un gain de temps et de ressources disponibles, permettant de maintenir et d’optimiser la performance des opérations au sein des entreprises.
Muda* = gachis en japonais